Duration: 10 hours
Team Members: 2
Skills Applied: Laser Cutting, Mechanical Systems Analysis, Sketching, Solidworks
Tools Used: Rabbit Laser Cutter
The aim of this project was to use a laser-cut acrylic part to hold 40lbs of weight. The rules specified there were two forbidden zones that no material for the hanger piece could pass or cross. The rules also specified that the hanger could only hang from the pegs.
The noticeable problem in this scenario was the thickness of the material. The thickness on the data sheet is specified to be 0.173 ± 0.01 in. Since acrylic has low yield stress, we decided to use 0.163in, the lowest value, for preliminary calculation. Since the compressive yield is higher than the tensile it was determined that the piece would likely buckle before yielding from compression.
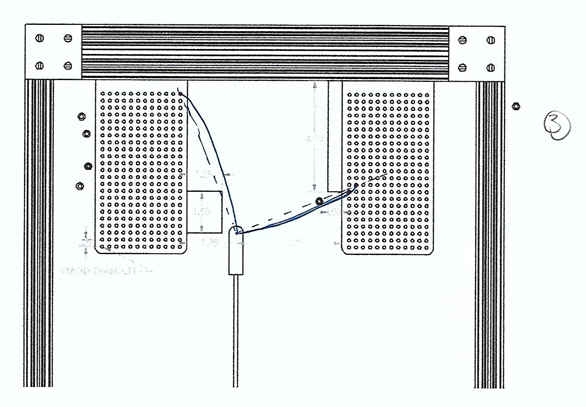
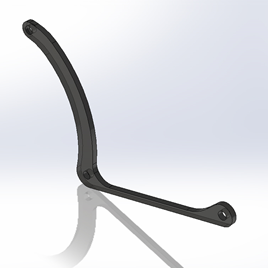
This design consists of a strong member that bears most of the weight and a smaller member that serves to counter displacements. The weight bearing section is curved to avoid the forbidden zone while also minimizing horizontal forces. The smaller member is thin and lightweight because experiences minimal stresses.
This design is suited to the task because it is able to bear the weight while also avoiding forbidden zones. The design consists of two major features, the strong arm and the supporting arm. The strong arm supports the vast majority of the weight, but as a result also undergoes more displacement. To counter this, the supporting arm serves to minimize displacements, and since this arm supports little weight, is has been minimalized in size and weight. These changes to our original triangular design allowed us to reduced approximately 40% of the weight from our initial iteration.
This design is suited for the task because the design has proven to be robust and reliable, while also remaining relatively lightweight. The FOS is 1.345, which leaves quite some room for things to go sideways.
Estimated mass is 13.2 grams.This was determined from the mass property in Solidworks.
Predicted failure is bending stress fracture, occurring on the inner radius on the left linkage.
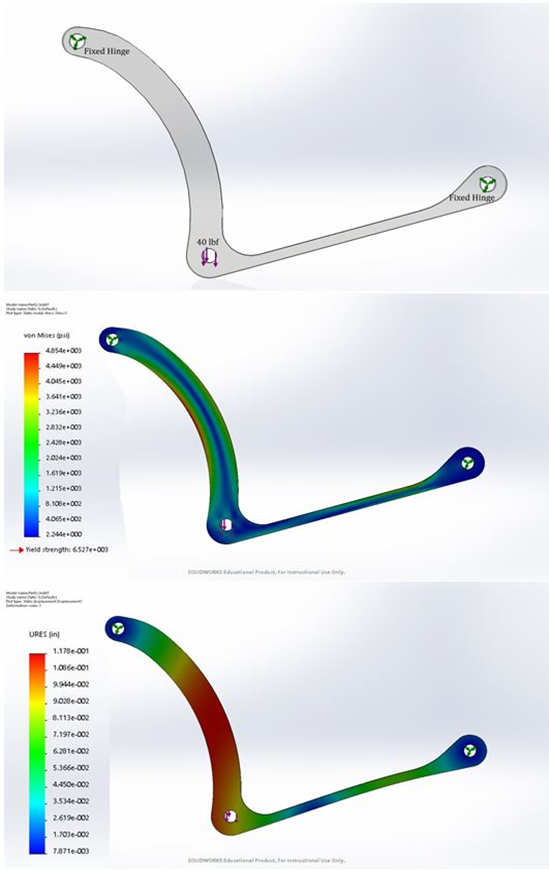
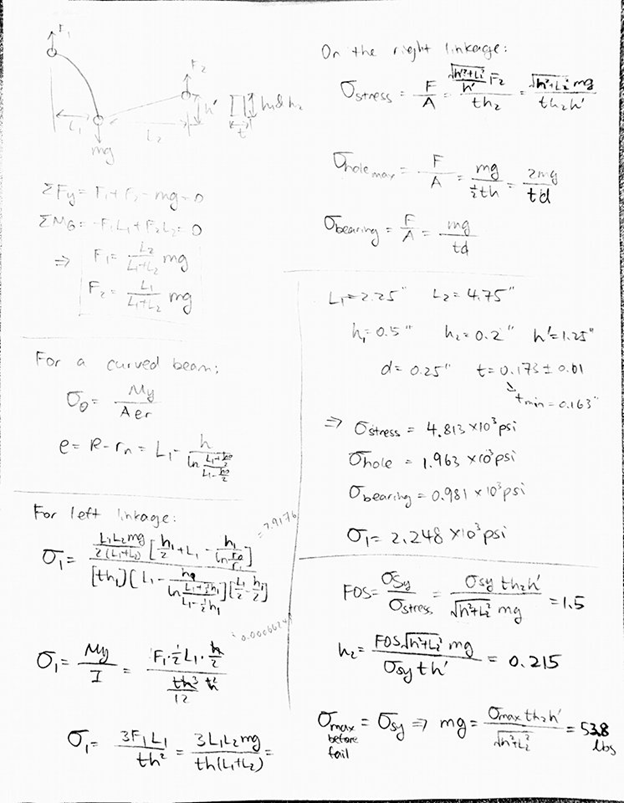
Documentation can be seen on the next page.